Cold working of metals is performed at or near room temperature so that the advantage of reduced yield strength, or forging pressure, accompanying elevated temperatures is not available to assist in the forming operation. Additionally, metals “work harden”, i.e., increase in yield strength, during deformation at lower temperatures, further adding to the work necessary to reach the desired shape.
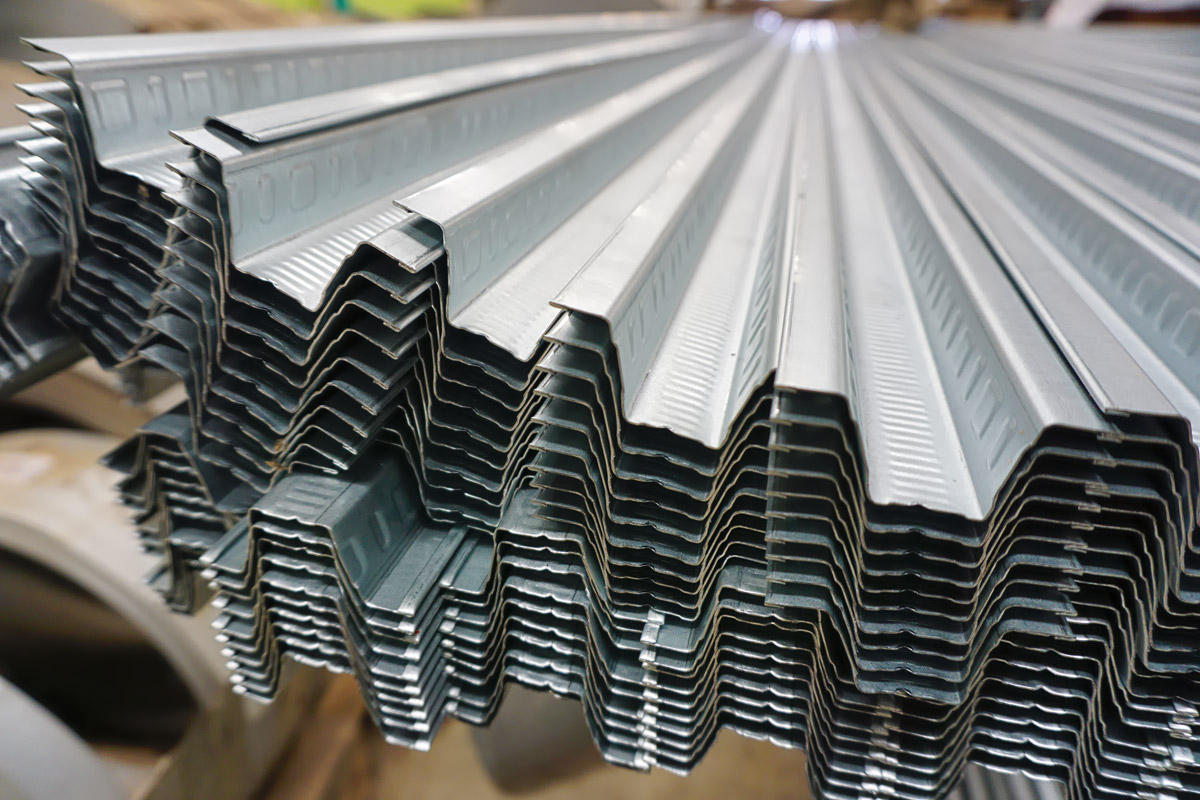
Benefits
The appeal of cold forming, in addition to the obvious cost savings when no heating is necessary, is the greater dimensional precision that can generally be achieved since there is no need to account for thermal contraction or distortion once the shaping is completed. And often just as important, the cold-worked metal part also avoids the surface discoloration (oxidation) that occurs at higher temperatures, so that the part may be presentable for sale and possibly service without further processing.
Limitations
The disadvantage to this process is that extremely hard (60 Rockwell C), highly abrasion-resistant die steel is required to endure cold working demands. With such an emphasis on abrasion resistance, the high hardness die steels are generally very brittle. The selection of cold working die steels offered by Finkl Steel are “mild” grades that provide some degree of fracture toughness over an exclusive focus on abrasion resistance.
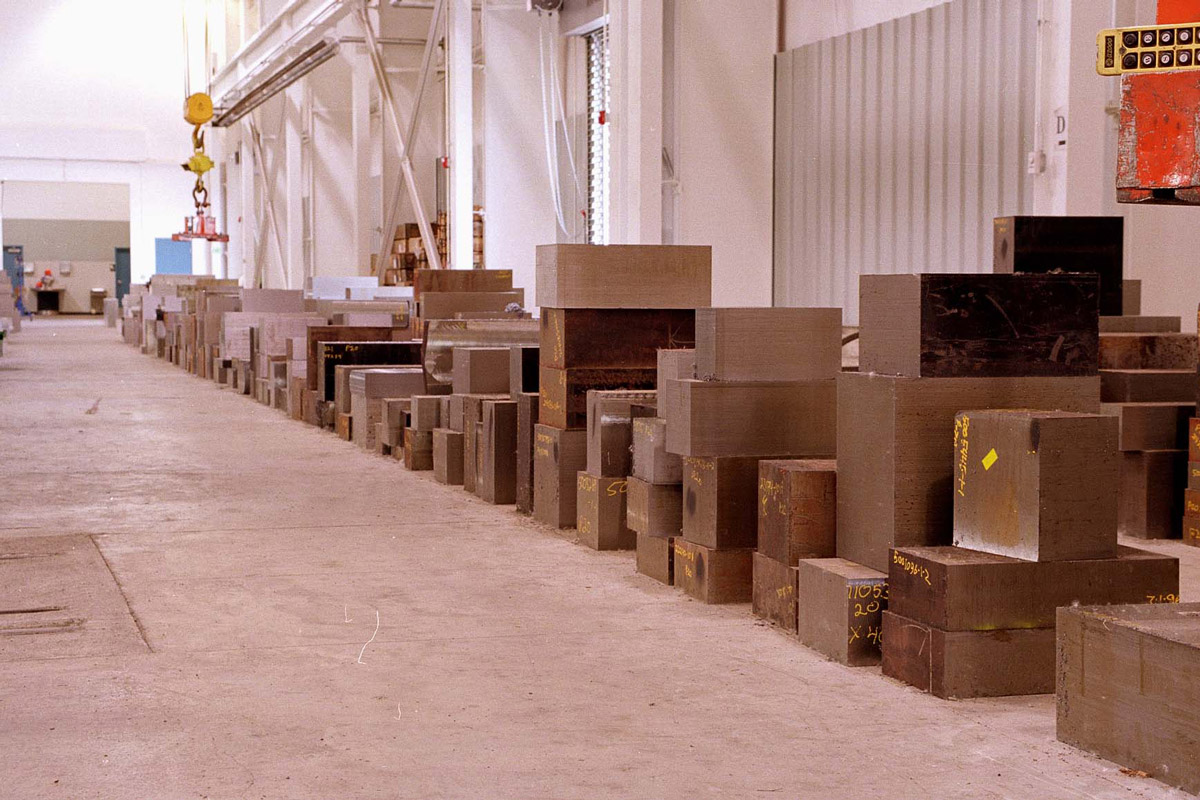
Material Grades
DOWNLOAD | GRADE | AISI | DIN | DESCRIPTION |
DRX® | S7 | 1.2357 | Lower Carbon (C 0.50%) with good wear resistance, but with a focus on mechanical “shock” resistance. Air Hardening | |
HLX ™ | This alloy provides high wear resistance and high toughness |